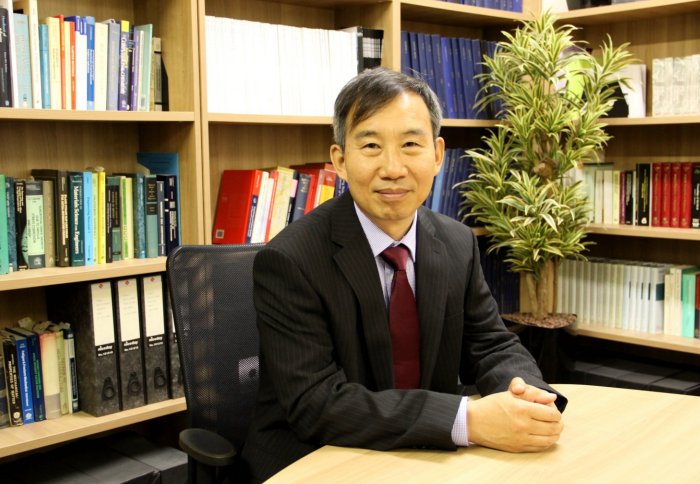

Last month, a company based on technology developed in the Department of Mechanical Engineering at Imperial opened a new factory in Coventry.
Impression Technologies Ltd (ITL) holds the trademark for Hot Form Quenching (HFQ®), a process of manufacturing complex-shaped, high-strength aluminium components for cars and other vehicles. The technology is based on the research of Professor Jianguo Lin, Head of the Mechanics of Materials Division in the Department of Mechanical Engineering at Imperial College London.
In this interview, Professor Lin explains how the company evolved, and how HFQ® helps make cars lighter and more environmentally friendly.
What problems in the industry does HFQ® address, and how does it work?
Automotive industries are trying to reduce fuel consumption and CO2 emissions, and one way to do this is to reduce the weight of the vehicle, which means you require less energy to drive it. One technique for reducing weight is to use lightweight and high strength materials, such as composites and aluminium. Ninety seven per cent of car components are currently made of steel, while aluminium full body structures are used only for expensive niche vehicles and premium cars. Replacing steel with aluminium can reduce weight by about 40-50 per cent, save about 20-25 per cent in fuel, and reduce CO2 emissions by 28-35 per cent. This data has been demonstrated, but the cost of using aluminium to manufacture panel components is currently too high, because aluminium is difficult to shape.
Fifteen years ago, when I was still at the University of Birmingham, we started developing a technology that combined heat treatment and forming of aluminium in one operation. This process enabled complex-shaped, high-strength panel components to be formed with high productivity and low costs, so that aluminium body structures could be used for all cars.
How did this technology turn into a company, and how did the university support you?
Imperial Innovations contacted me to ask about research that could potentially be turned into a business; I mentioned to them that one of our patents was the HFQ® technology, and they found it very interesting. After an independent market research and a number of meetings discussing the possibilities of this technology, they decided to provide seed funding for Impression Technologies, and we established the company. HFQ-formed parts have now been used for a number of car models already on the road. We set up our first automated production lines with an investment of about £5 million and collaborations from many other companies. The next step is to try and use the technology for mass production of popular cars.
I’m a board member of the company, and we still have many related research projects here at Imperial. We organise an HFQ® research day with key people from the company, to keep them informed about our work, and to find out about the scientific problems they get from customers. This helps us define better, more applied research projects with interesting scientific challenges.
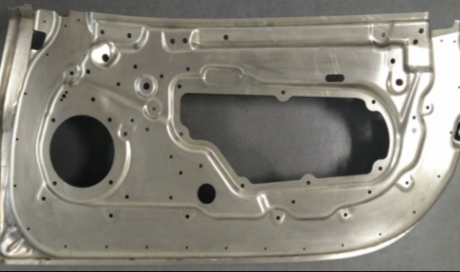
HFQ technology creates high-strength aluminium components
What does the opening of a new facility mean for the company?
Automotive companies want to see whether their components and their complex designs can actually be made, so the company opened a new factory for demonstrations. Impression Technologies is a high-technology company, they only do research and development work and small batch production, not mass production, at least not at this stage. This new production line will help them make sure that individual components can be made with HFQ®. Afterwards, car designers can subcontract to component manufacturers for mass production, using the technology provided by ITL.
What were the breakthroughs and obstacles in developing HFQ?
Our expertise combines the science of materials, manufacturing technologies and mechanics of materials, it is multidisciplinary research. We found that this was the right way to achieve what could not be achieved before. We have demonstrated that this technology can manufacture complex-shaped components nobody else could manufacture before, but to enable it to be used widely in the increasingly competitive automotive industry, we need to reduce costs further. Over the next three years, we will try to reduce costs by another 25 to 30 per cent through further development and optimisation of the materials processing route, manufacturing technologies and tooling.
What advice would you give to other researchers who want to commercialise their work?
I would encourage others to think about commercialisation at the beginning of their research. This would help them choose appropriate research projects. The help from Innovations is great, without them it wouldn’t be possible to set up a company.
What is the importance of international connections for developing HFQ® and putting it into practice on a wide scale?
We already have two European projects going on, encouraging the rest of the world to use and research these technologies. We also have many collaborators outside of the EU, in Japan, South Korea, China, etc., to carry out research and further development, to enable a wider range of alloys to be formed, and to reduce costs even more. We are connected with the supply chains of automotive and aerospace companies, with tooling suppliers. It’s a system, not just one technology: you need manufacturing facilities, materials, tooling technologies, etc. We’ve established connections with supply chain companies. The next step is to form an HFQ international club or society; about 50 companies and universities are involved now.
What do enjoy most about your work? What made you choose this research area?
I like scientific and technical challenges in research, and I try to do things that bring me personal satisfaction. If I develop something new that people like, and it can be used in practice, I feel happy about it. I believe that’s the main driving force, and I think many researchers are similar to me.
Article text (excluding photos or graphics) available under an Attribution-NonCommercial-ShareAlike Creative Commons license.
Photos and graphics subject to third party copyright used with permission or © Imperial College London.
Reporter

Nadia Barbu
Department of Mechanical Engineering
Leave a comment
Your comment may be published, displaying your name as you provide it, unless you request otherwise. Your contact details will never be published.