Cultivated meat startup Multus raises £7.9m
Developing affordable growth media products for the nascent cultivated meat industry will bring forward climate and animal welfare benefits.
Multus Biotechnology has raised £7.9 million from investors to support further R&D on growth media for cultivated meat and the transition to manufacturing its first commercial products. The company was started a little over three years ago by four students in the departments of Life Sciences and Bioengineering, who met through Imperial’s Synthetic Biology Society.
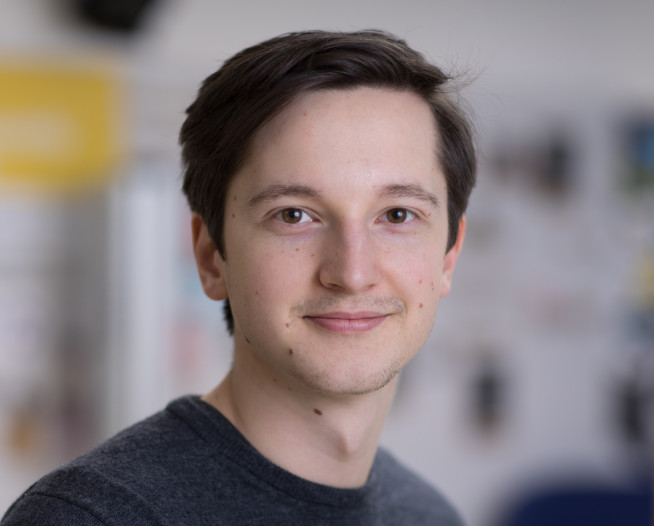
“There is a huge opportunity in cultivated meat, but still some fairly large technical challenges in getting to scale and price parity with farmed products,” says Cai Linton, co-founder and chief executive of the company. “A solution to those challenges, designed for the food industry, doesn’t really exist, so we want to create that.”
The announcement follows the company’s selection in June 2022 for a European Innovation Council (EIC) Accelerator grant. These prestigious and highly competitive grants, worth up to €2.5 million (£2.1 million), support startups and small companies developing and scaling up game-changing innovations.
“We are the first cultivated meat company ever to have had funding through this scheme,” said Mr Linton. “Having this signal that there is public money behind our project, and that the European Commission is behind it, has definitely benefitted our fund raising.”
A growing industry
Cultivated meat is produced from animal stem cells, which remain viable indefinitely when cultured and stored under the right conditions. Placed in a bioreactor, and fed with a cell culture medium containing basic nutrients and growth factors, these cells will multiply. By varying the medium, and providing some structure, the cells will diversify and develop into tissues equivalent to meat.

This method of meat production avoids the animal welfare issues of conventional farming, and promises multiple environmental benefits. A life-cycle assessment produced last year by environmental consultants CE Delft looked forward to 2030, and found that cultivated meat would have much lower carbon footprint than farmed meat, as long as sustainable energy sources were used. Meanwhile, consulting company McKinsey reported that the world market for cultured meat could reach $25 billion (£20.5 billion) by 2030, if consumers take to the products.
There is a huge opportunity in cultivated meat, but technical challenges in getting to scale and price parity with farmed products. Cai Linton Multus Biotechnology
The four students behind Multus – Cai Linton, Kevin Pan, Reka Tron, and Brandon Ma – started out by asking a simple question about cultivated meat. The science for producing it is proven, and the benefits for climate change and animal welfare are undisputed, so why can’t we go to the supermarket and buy some?
One answer was that the blood serum typically used as a growth medium was all wrong. First of all, it is expensive, having been made to the exacting standards demanded for biopharmaceutical and biomedical research. And second, it is generally derived from animals, which undermines the animal-free aspirations of the cultivated meat industry.
So, they set out to streamline the serum production process and explore more efficient ways of providing cell nutrition using plant-based ingredients. Their goal was to develop a replacement growth medium that would be animal-free, inexpensive and possible to produce in large quantities.
From hackspace to incubator
Multus took its first steps in Imperial’s Advanced Hackspace, while participating in initiatives such as the Faculty of Natural Sciences Make-a-Difference competition and the Enterprise Lab Venture Catalyst Challenge. It also passed through the Climate Launchpad programme, which has since evolved into The Greenhouse, an accelerator run by the Undaunted partnership between Imperial's Grantham Institute and the Royal Institution.
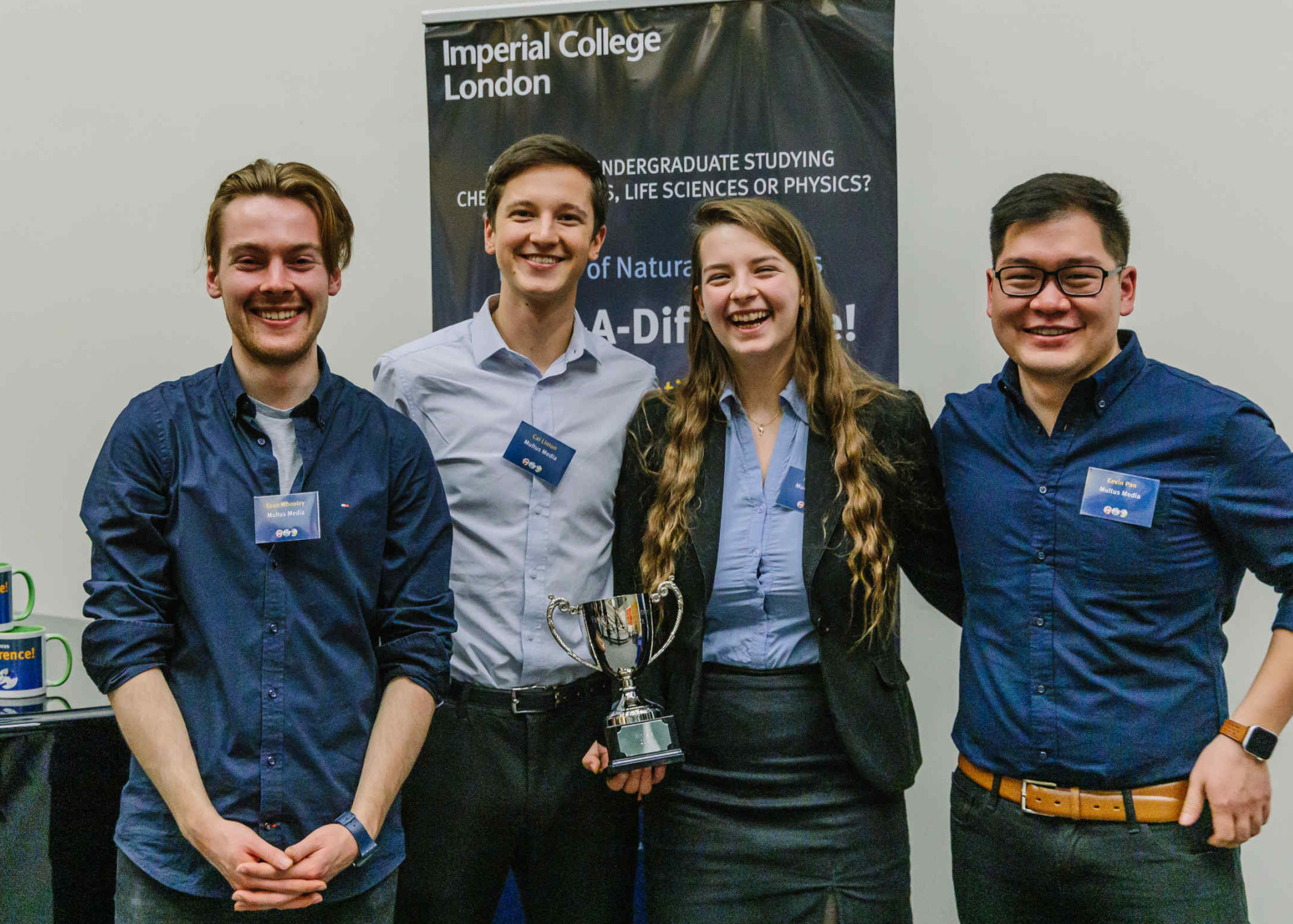
In 2020, Multus moved to the Translation & Innovation Hub (I-HUB) on Imperial’s White City Campus. Around the same time, it also won a place at IndieBio New York, an accelerator programme for life science startups backed by venture capital. This provided funding to develop a first product and prepare for the next phase of fundraising. This took place in the first half of 2021, and attracted £1.6 million from investors and UKRI enough for Multus to bring its first product, Proliferum M, to the market.
Meanwhile, it entered the European Institute of Innovation and Technology (EIT) Food Accelerator Network, which targets companies with a prototype that have not yet reached commercial scale. “That was a really valuable experience,” Mr Linton says. “We learned a lot about how we innovate in business models, grow our team, and think about internationalisation. Now we are working across Europe on the different collaborative opportunities we discovered through the programme.”
In a similar way, Asian connections are being made thanks to the company’s participation in the Singapore Global Incubator Programme, funded by Innovate UK.
A complex market
Addressing such a new market as cultivated meat has been a challenge. “Because we are in a new industry, we need to do a fair amount of innovation on the business model side, building the right relationships and finding ways we can add value to different kinds of companies, at different stages of their own development,” Mr Linton says. “So, we are pushing the industry forward at the same time as our own company is scaling and growing.”
The company’s first product was designed for research use, not commercial meat production. “Proliferum M is mostly sold to early-stage companies doing a lot R&D, and we can be a partner for them as they scale up, from lab to bioreactor. But we also want to tap into later stage companies, for example with the ingredients we are designing and producing in-house, which are more like raw material inputs to a supply chain.”
The funding raised this year will support the company as it develops follow-up products for commercial meat production. “Our goal is to have growth media for chickens, cows and pigs that can help companies get products on the market. That means we have to scale-up internally, get larger customers on-board, get regulatory and standards approval, and have our manufacturing facility operating.”
These cultivated meats are priorities because of the urgency in reducing factory farming in these markets. “Then we will work with other partners on seafood and other cell culture types on a more custom basis.”
Innovative manufacturing
Meanwhile, the EIC grant will play an important role in developing the manufacturing facility, which will be a significant innovation for the food industry. “We need a manufacturing capacity that meets scale, cost and food safety requirements, which is something that doesn’t exist today,” Mr Linton says. The goal is to have the manufacturing facility up and running in mid to late 2023.
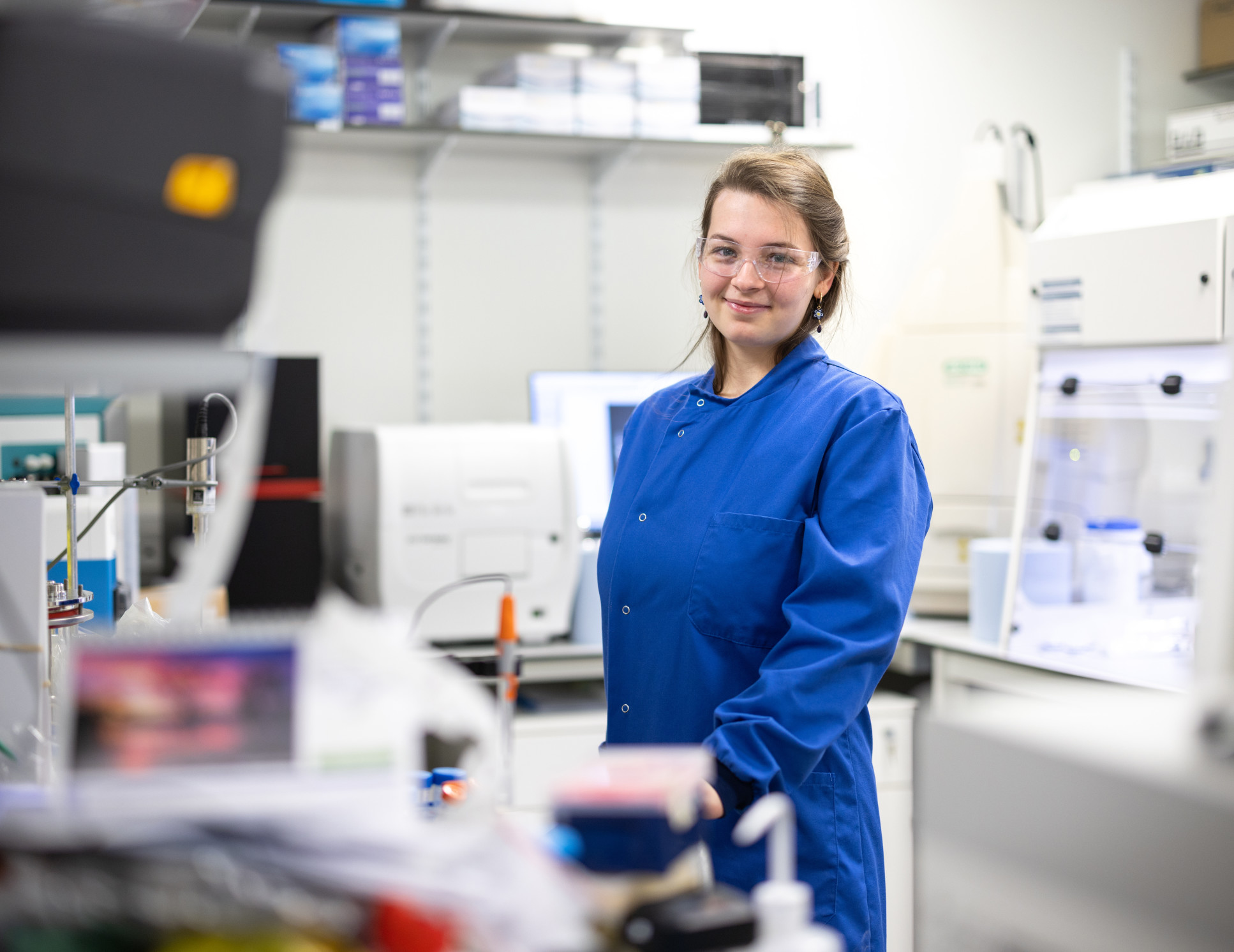
Since the UK has not yet joined the EU’s Horizon Europe programme, of which the European Innovation Council is a part, the project now being funded by UKRI via the Horizon Europe Guarantee.
Mr Linton expects Multus to double in size over the next 18 months, to around 25 people. “Hiring is always on our mind, in technical and non-technical areas. We want to work with people who are committed to solving climate change and working in the food industry.”
This is one reason he is keen for the company to retain a close connection with Imperial. “We will need to expand out team in technical areas, and being close to Imperial is fantastic for that,” he said. “So, we will be looking for software engineers, bioprocess engineers, cell biologists, synthetic biologists, chemists, and so on.”
Supporters
Article text (excluding photos or graphics) © Imperial College London.
Photos and graphics subject to third party copyright used with permission or © Imperial College London.