Electric mobility
The journey to an electric future
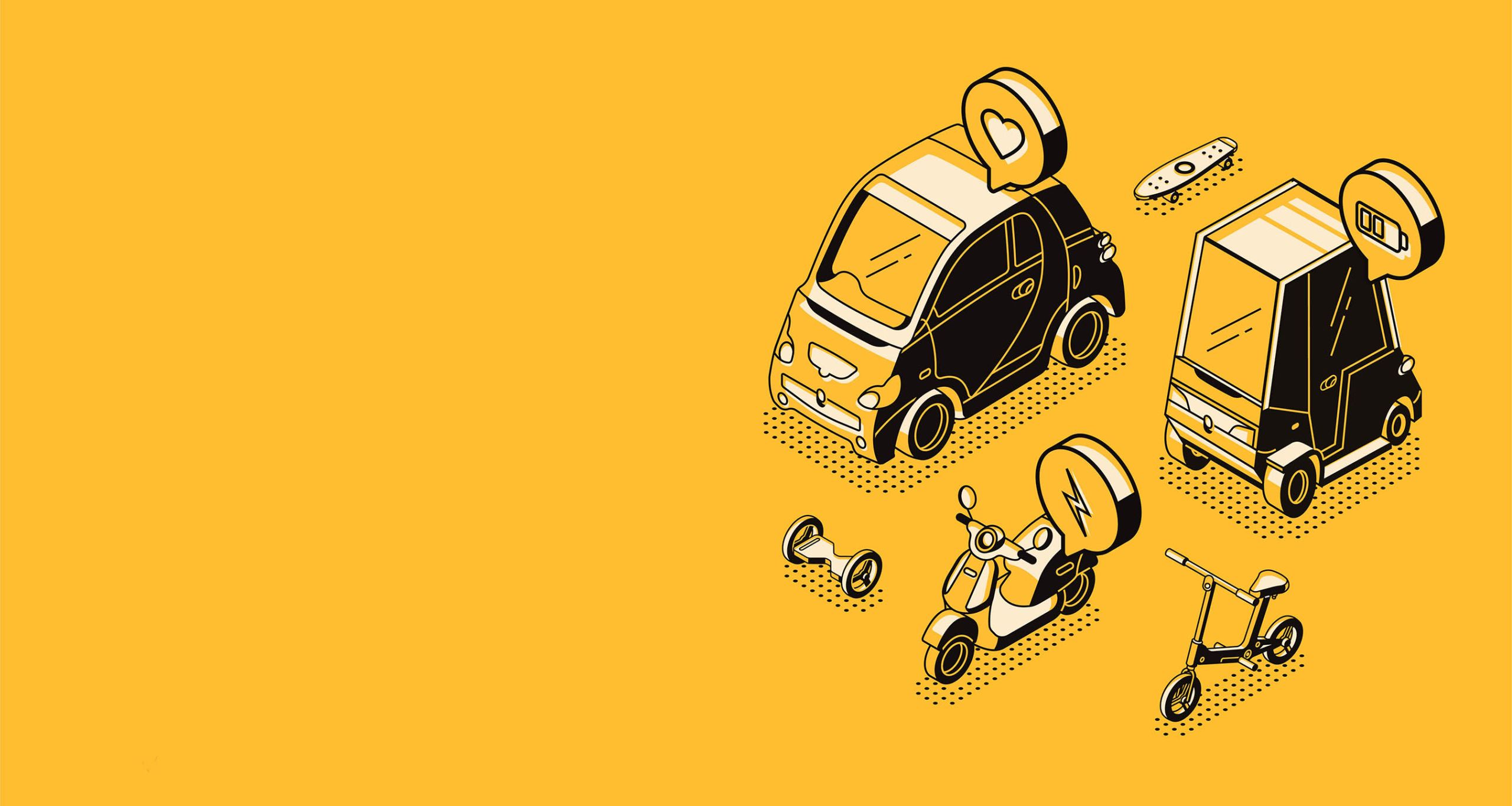
It is hard to overstate the impact that electric transport could have on the world. Most existing modes of transport are driven by combustion engines, which have dictated how we design cars, ships and planes, and where we place refuelling stations. The oil which fuels them has shaped global infrastructure and geopolitics. But oil is polluting, and running out.
We cannot rely on good intentions alone. Electric vehicles need to provide a comparable, or better, experience to their fossil fuel-powered counterparts.
A wave of electrification is underway, most prominently in electric cars, and gradually moving to trucks, ships and even planes. Moving from filling our vehicles with oil derivatives to plugging them into the grid will change how we design cities and energy systems. “Getting to that point requires a complex mix of cross-disciplinary innovation and policy levers,” says Professor Tim Green, Co-Director of the Energy Futures Laboratory (EFL), which facilitates research across Imperial on a range of energy challenges.
“We cannot rely on good intentions alone. Electric vehicles need to provide a comparable, or better, experience to their fossil fuel-powered counterparts. The technology to do this in cars is pretty advanced, but there is plenty of room for further improvement, and much to be done before we can see some degree of electrification in heavier vehicles. On top of that, we need new approaches to infrastructure and energy distribution.”
If we get this right, there are huge benefits to be reaped. A global electric transport system could significantly reduce greenhouse gas emissions without compromising our standard of living. Research across Imperial is helping us get there.
Electric goes mainstream

The starting point for the electric transport transition has to be the car. It is where most progress has already been made, and its success – or otherwise – will blaze a trail for the electrification of other areas of transport.
Electric vehicles (EVs) are growing in popularity. Right now there are around 265,000 EV owners in the UK, and National Grid projections suggest that could rise as high as 36 million by 2040 as anticipated restrictions on petrol vehicles kick in. The future looks bright for electric mobility, but the hoped-for progress still depends upon engineers and scientists addressing important challenges.
Better battery life: Reducing range anxiety
One consistent reason people give for not making the switch to EVs is the worry that the battery will run out and leave them stranded, or, perhaps more realistically, saddle them with a half hour wait at a charger mid-journey.
Dr Gregory Offer, of Imperial’s Faculty of Engineering and The Faraday Institute, is researching new ways to design batteries that could lead to major advances in range and durability.
“EV batteries are made of lots of cells. The problem with much of the current battery research is that it focuses on packing as much energy density as possible into individual cells,” says Dr Offer. “But we found that this process creates problems that reduces overall efficiency of the battery as a whole. If we redesign the whole system – the way the battery is put together - we could add 10-15% density, which could mean 10-15% longer range for EVs."
Dr Offer is part of a team at the Faraday Institute that brings together materials scientists, electrochemists, engineers, modellers and other to explore battery performance. This multidisciplinary approach allows them to look at problems from new perspectives and identify improvements that others miss.
This is a truly disruptive advance. Our research suggests that this work could lead to a 10-15% range increase, 200% longer lifetime through reduced degradation, and 15-20% cost reductions. The total cost of ownership could be reduced by 60-70%.
One promising improvement being made possible from this whole-system approach is heat transfer. “We started building models of heat transfer within battery systems,” says Dr Offer. “We developed a new metric, cell cooling co-efficient, which measures how easily heat can be rejected.”
This allowed the researchers to model how individual changes in layout, or material use, would affect the overall system.
“We found that much of the work optimising sub-systems of batteries has actually been detrimental to the system as a whole. In particular, cramming lots of energy dense parts as close together as possible created heat traps which harmed overall performance.”

Nissan Leaf chassis with battery pack at the 2009 Tokyo Motor Show. Photo: Tennen-Gas / CC BY-SA
Nissan Leaf chassis with battery pack at the 2009 Tokyo Motor Show. Photo: Tennen-Gas / CC BY-SA
By redesigning cells to remove thermal bottlenecks and allow the heat to be properly moved out of the battery, the system as a whole can operate more efficiently.
“This is a truly disruptive advance” says Dr Offer. “Our research suggests that this work could lead to a 10-15% range increase, 200% longer lifetime through reduced degradation, and 15-20% cost reductions. The total cost of ownership could be reduced by 60-70%."
“It’s really a win-win-win. If widely adopted it should significantly accelerate electrification in EVs, as well as other sectors that use energy storage. We really are hoping to trigger a revolution in the battery industry with this work.”
The next stage is for industry to adopt this understanding. There are already promising signs thanks to the Faraday Institute's links to industry.
More efficient driving
Electric vehicles may be greener than their internal combustion engine equivalents. But they still need energy, some of which is generated by fossil fuels. The less of it they use, the better.
Dr Simos Evangelou, of Imperial’s Faculty of Engineering, is looking at how EVs can be driven more efficiently.
“We have long been modelling how vehicles work, and how to improve fuel efficiency through optimising control systems. As we move to electric, this work will take on ever greater value,” says Dr Evangelou.
As we move toward intelligent on-board software and connected infrastructure, we can look at changing driving behaviour to adjust to surroundings, such as incremental speed changes for when a traffic light is about to change.
When a driver presses the pedal, control systems take the optimal decisions on how to provide the energy to accelerate the vehicle in accordance with the foot pressure. Having modelled the interactions of control systems across different vehicles, including vehicles that have multiple energy sources in their powertrains, Dr Evangelou and his team have developed algorithms that can be embedded into on-board software to provide optimal control decisions in real time.
These can either automatically make imperceptible efficiency alterations, or provide advice to the driver which nudges them towards more efficient driving.
This work started long before EV’s were a serious proposition, but EVs are now changing the game. Combustion engines use controlled explosions of petrol to drive pistons and create movement, and a separate battery for lights and other functions. In EVs, the battery uses electric current to create propulsion and also power on-board electric systems. This creates more opportunity for precision management of control systems: allowing not only more efficient power transfer, but also better comfort and safety, for example through electric actuators that control car suspension to adjust to road conditions.
“Control system software can help improve individual driving efficiency,” says Dr Evangelou. But that’s just the beginning. “As we move toward more intelligent on-board software and connected infrastructure, the opportunity becomes even bigger. We can look at changing driving behaviour to adjust to surroundings, such as incremental speed changes for when a traffic light is about to change. In the longer term, we could see these systems optimising electric autonomous fleets and even self-driving cars.”
Environmental concerns: Mapping the impact of electric vehicles
Some suggest that electric vehicles are just as polluting as conventional vehicles, since they are recharged using electricity generated by fossil fuels, and their batteries create emissions from mining and their manufacture. Research at Imperial and many other institutions suggests this is not the case.
A meta-analysis led by Dr Iain Staffell, in Imperial’s Centre for Environmental Policy, reviewed academic studies of battery manufacture and data on Britain’s electricity generation mix from Drax Electric Insights. They found that producing the energy to charge an EV in Britain produces 75% less CO2 than is emitted by equivalent petrol or diesel vehicles, showing them to be far greener at the point of driving.
Battery manufacturing is an energy and carbon intensive process. But the same research showed that an EV battery’s carbon emissions are paid back over its lifetime in virtually all countries. With Britain’s current electricity mix, smaller electric cars and vans take 2-4 years to save the amount of CO2 emitted in making their batteries. Larger luxury models take 5–6 years. Payback is much faster for high-use vehicles such as taxis and delivery vans. After this period, they are lowering the overall life-cycle carbon emissions compared with fossil fuel equivalents.
Beyond the car

The electrification of cars is starting to shine a light on the need to electrify other areas of transport. These come with their own challenges.
Powering fleets of scooters
A full charge these days will usually power an electric car for a few days of commuting, making range less of an issue for most.
This is not the case for high-use vehicles, such as taxis and delivery vehicles. Current batteries will not last for a whole day of constant driving. And since income relies on vehicle access, time spent finding, queueing for, and using chargers present issues.
One solution could be wireless charging. Wireless pads could be placed where vehicles naturally stop, such as taxi ranks, lunch stops and delivery entrances, allowing vehicles to keep topping up when they are naturally stationary.
We could place wireless changing pads at strategic locations such as outside busy takeaways.
“An interesting application of wireless charging is for electric scooters,” says Paul Mitcheson, Professor in Electrical Energy Conversion at Imperial.
Scooters are a growing feature of modern cities, zipping about to deliver takeaways to people’s doors. Electrifying these could create greener, quieter cities. But they can only carry small batteries, and their riders need to make high volumes of deliveries to make a reasonable wage. Regular stopping for a 20-minute charge would be an imposition.

Scooters are a growing feature of modern cities. Photo: Michael Vi/Shutterstock.com
Scooters are a growing feature of modern cities. Photo: Michael Vi/Shutterstock.com
“We could place wireless changing pads at strategic locations such as outside busy takeaways”, says Professor Mitcheson. “If they had to plug in every time they stop, it wouldn’t be worth it. But if they just get a few minutes charge whenever they stop, without doing anything, that would be enough to keep them going.”
Early wireless charging technology already exists for electric cars, but it is too heavy and bulky to work for scooters.
“This might sound like a challenge of scaling existing technology,” says Professor Mitcheson, “but at an electronics level it actually needed a totally different approach.”
In wireless charging, the transmitter contains a loop of wire. When an A/C current is applied to that wire, it produces a changing magnetic field, creating an energised zone around the transmitter. That zone can induce a current into another loop of wire within the receiver, which then charges the battery.
The distance allowed between the transmitter and receiver for efficient operation is complex but related to both the size of the loop and operating frequency.
Most inductive charging, such as that used for phones, uses low frequencies of around 100 kHz. Low frequency charging is easier from an electronics perspective, but creates a small zone where the system is efficient. So you either need very big loops, or the receiver needs to be positioned within a very precise area to work.
By increasing the frequency significantly to the MHz region, and with considerable fine tuning of electronics, Professor Mitcheson and his team could redesign the system to create a much broader efficient charging zone, allowing charging at much greater distances, and so more freedom for receiver positioning.
“This approach opens new opportunities for charging things like scooters – as well as bikes or drones - where you need a lightweight receiver, and you need it to work without the bike being too precisely positioned”, says Professor Mitcheson.
He is currently looking at launching a startup to commercialise the technology.
Freight by sea and land: HGVs and shipping
From the small, to the very big. We already see vans and even buses electrified, but what about really big vehicles such as large HGVs, construction vehicles, and freight ships?
Full electrification is, at best, a distant possibility. But some level of electrification is possible in the near term through hybridisation. And by combining electrification with low-carbon fuels, these large vehicles could still get towards net zero emissions.

Illustration of a hybrid HGV at a charging station. Image: Chesky/Shutterstock.com
Illustration of a hybrid HGV at a charging station. Image: Chesky/Shutterstock.com
Hybrid vehicles use an electric motor to create a propulsion, as opposed to one driven by combustion. This, alongside other on-board electronics, is powered by multiple power sources. Ideally, power comes from batteries, renewables, or recovery of waste heat from the vehicle. But, in addition, a separate generator provides power for when these clean sources cannot deliver.
Decarbonising heavy vehicles is much more challenging than smaller electric vehicles, and their success depends upon reducing their weight and size, and increasing energy density.
Electric motors allow greater control of vehicle propulsion, and more efficient transfer of energy, than internal combustion engines. Electrification also supports advances in autonomy and platooning which could improve efficiency further. So, switching to electric motors is valuable in its own right, even if powered by fossil fuel generators.
Since batteries are a long way off for such large vehicles, a better route to lowering emissions could be to use generators powered by net zero fuels, such as hydrogen or ammonia instead of petrol of diesel. Net zero fuels can be generated in various forms, such as combining sequestered CO2 with renewably generated hydrogen.
“We certainly envision these as future options”, says Professor Martinez-Botas in the Department of Mechanical Engineering. “Putting electric propulsion in these vehicles is not too challenging, but we need more compact and power dense fuel cells, and routes to producing those net zero fuels at scale, in order to enable a low-carbon pathway.”
This is an area where his team at Imperial can help. They have long worked with manufacturers of long-haul trucks, and marine engine developers, on thermofluids – the study of how air, fuel and heat are transferred around systems. Imperial has a number of world-leading facilities for engine testing under realistic airflow conditions.

Professor Ricardo Martinez-Botas displays an invention designed by Imperial's Turbocharger Group. This active component recovers energy that would otherwise be wasted in an internal combustion engine. Photo: Layton Thompson
Professor Ricardo Martinez-Botas displays an invention designed by Imperial's Turbocharger Group. This active component recovers energy that would otherwise be wasted in an internal combustion engine. Photo: Layton Thompson
Work so far has focused on optimising combustion engines, by fine-tuning air intake and recovering energy from hot exhaust gases. But these same approaches can help plan future hybrid vehicles and investigate fuel cells that could power hybrid electric ships and trucks.
Hydrogen fuel cells, for example, combine hydrogen and oxygen to create electricity and water. Their efficient functioning involves pumping air in and water out, and right now these processes have very high efficiency losses. Imperial’s systems can help optimise this pumping, and assess opportunities for waste heat recovery, making these fuel cells more commercially viable.
Professor Martinez-Botas says “Decarbonising heavy vehicles is much more challenging than smaller electric vehicles, and their success depends upon reducing their weight and size, and increasing energy density.”
“We are starting to look at how our existing research facilities can be used to optimise fuel cells. This is just one part of the picture in fuel cell development, but an important one. We are just at the start of this journey, but we are on it”.
Can we dream of electric planes?
Electric planes sound like a far-off dream. Can we really replace those big fuel powered engines with batteries, and trust them to fly us around the world?
For the moment, the short answer is ‘no’. Current battery technology is simply too heavy to replace engines on commercial airliners.
But there are opportunities. “In small regional aircraft, the numbers add up,” says Dr Rafael Palacios, Professor of Computational Aeroelasticity in Imperial's Department of Aeronautics.
Current flight simulators are built around the aerodynamics of existing aircraft designs. But these are no use for completely new designs, which will respond in completely different ways to pressure changes or high winds. there’s a need to go back to fundamentals to create new dynamic response models.
Other possibilities come from hybrid models. Planes could combine batteries with a fossil fuel generator as a transition technology. Solar planes are also attracting a lot of interest, with large PV covered wingspans generating power in flight and so reducing the need for heavy batteries.
But electric flight is not simply a case of replacing a jet engine with a battery-powered one.
“Whichever route we go towards electrification, we’re going to need to rethink the plane,” says Dr Palacios. “That means looking at weight reduction, changing where propulsion comes from, where the engine sits, the wingspan. All those decisions change the aerodynamics of the aircraft.”
“Designing these new planes will be about managing many trade-offs to make things work both aerodynamic and structurally with the new power systems,” says Dr Palacios. “If we replace a jet engine with electric motors, that allows very different configurations, such as using lots of small motors rather than two large ones, since electric motors can easily scale up or down.”

NASA engineers put the X-57 Maxwell, NASA's first all-electric X-plane, through its initial telemetry tests at NASA's Armstrong Flight Research Center in California. Photo: NASA/Ken Ulbrich
NASA engineers put the X-57 Maxwell, NASA's first all-electric X-plane, through its initial telemetry tests at NASA's Armstrong Flight Research Center in California. Photo: NASA/Ken Ulbrich
To support this possibility, Dr Palacios and his team are developing mathematical models that can help designers of a new breed of aircraft understand how it will fly.
“Aircraft prototypes are hugely expensive. You can’t just fly it and see if it works, because if it doesn’t, it will cost you a fortune,” he says. Instead, early work is simulated.
This is no easy task. Current flight simulators are built around the aerodynamics of existing aircraft designs. But these are no use for completely new designs, which will respond in completely different ways to pressure changes or high winds.
There’s a need to go back to fundamentals to create new dynamic response models. “Everything that goes in is a law of physics,” says Dr Palacios. “We are working with atmospheric models, materials structure models, physical models, and aerodynamic models. By combining all that within the right mathematical architecture we can start to predict how these new plane designs will respond to flying conditions.”
These models will allow designers of a new breed of aircraft to understand aircraft behaviour, test and refine ideas, and make evidenced design choices.
“This is an emerging area and there is much work to be done,” says Dr Palacios. “But if we are to ever realise the dream of electric flight, we will need to design planes in a whole new way. Computer models are the start of that.”
Powering the transition

Electrifying the world’s cars, let alone planes and ships, requires a major shift in how we wire the world. Most vehicles are powered by energy extracted by combustion engines from oil and gas that has been shipped around the world. This will be need to replaced by energy generated at power stations and delivered through cables.
“This,” says Goran Strbac, Professor of Energy Systems, “is not quite as big a problem as it sounds. In fact, it is a huge opportunity for decarbonisation.”
Professor Strbac looked at data from the Department of Transport and calculated how much energy would be needed if drivers switched to EVs. He found that the grid could comfortably cope with the demand without needing significant increase in energy generation capacity.
“The challenge is managing that demand” he says. “If everyone wants to charge their car from 8-9pm that would double peak demand and place a huge strain on the grid, requiring network reinforcement and doubling the amount of generation capacity. But if they are flexible about when they charge, generation can be easily managed.”
The way to do this is with smart charging, smart system integration, and smart tariffs to incentivise people to charge at certain times. EV drivers arrive home and plug in their cars and set a time for when they next need it. Energy suppliers then use this data to carefully match vehicles charging times, which is in any case at low demand during the night when most people charge.
If we have thousands of vehicles connected to the grid at any one time, that is essentially a massive backup battery for power generators... It could even make sense to pay people to switch to smart EVs.
But smart charging does not only allow a managed transition to EVs. It also presents a huge opportunity.
“If we have thousands of vehicles connected to the grid at any one time, that is essentially a massive backup battery for power generators. They can buy back small amounts of energy from each car – and we are talking small amounts, say 1% per battery over ten minutes – whenever they need it.”
Right now, the grid has to operate build in backup using gas generators so that it can cope if one power station goes offline. It also increasingly needs to be able to deal with the intermittent nature of wind and solar energy generation.
“If the grid had a huge battery to draw on, that changes the game”, says Professor Strbac “In case of an unexpected loss of generation, we just draw power from EVs for ten minutes”.

Electric car charging station. Photo: BigPixel Photo/Shutterstock.com
Electric car charging station. Photo: BigPixel Photo/Shutterstock.com
His team demonstrated that smart charging and ‘Vehicle to Grid’ (V2G) could reduce the need for investment in backup gas plants and make better use of renewable resources. One study, with DECC and BEIS, showed that flexibility technologies and control systems (including V2G) would deliver the same long-term carbon reduction target as building 10 gigawatts nuclear and 15 gigawatts of offshore wind. This is achieved by reducing distribution network reinforcement and investment in peaking plants (power plants which only run when there is high demand), leading to overall savings of £8 billion per year. Another study calculated that electric vehicles would deliver a 60-tonne reduction of CO2 emissions from energy generation per year.
“That’s such significant value, it could even make sense to pay people to switch to smart EVs,” says Professor Strbac.
The benefits are clear, and the next question is how to make all this work. “We need to think about it holistically and how to get there cost-effectively,” he says.
Here, work is still needed. There are challenges around when to invest. We need more EV owners to make this work, which means more investment in charging infrastructure. But there is a reluctance to invest in charging infrastructure without more EV owners.
There also needs to be more thought around what that infrastructure looks like. Lots of vehicles connected to slow chargers for 8-10 hours, overnight or at work, creates lots of room for smart energy management. Vehicles connecting to rapid chargers for half an hour at peak times does not.
We can incentivise slow charging and off-peak times, but this is not a solution for fleets, long haul, or public transport, which need to drive all day, or for people without access to a home charger. Public charging infrastructure also needs to deal with this challenge, for example by building dedicated charging stations part-powered huge batteries that are charged overnight, and so introduce much more flexibility.
“There are still plenty of challenges to overcome,” say Professor Strbac. “But there is no doubt that smart charging and electrification of transport represents a huge environmental opportunity, and a huge economic one for the low carbon energy system. It will need some big picture thinking, long term investment, and collaboration from lots of different parties to get there.”
On the road to an electric mobility future
Electrification has come a long way in just a few years. Research is advancing rapidly across the board, from battery power, to electric propulsion systems, to rethinking our entire energy and transport infrastructure for an electric vehicle future. It is even touching vehicles too heavy for batteries, thanks to innovative thinking around hybrid approaches that could realise the zero-carbon vision of electric vehicles.
Electrification of transport now has significant momentum. Just a few years ago, it was hard for many to believe researchers’ claims that electric cars could soon become mainstream. Now that seems almost inevitable. Today’s research will power a new generation of ever improving electric vehicles and support the transition to a low carbon future.
This feature was commissioned by the Imperial's Enterprise Division.
The Enterprise team helps businesses to address their challenges by accessing the College's resources, talent and expertise - and helps academics and students find new ways to turn their expertise into benefits for society.
