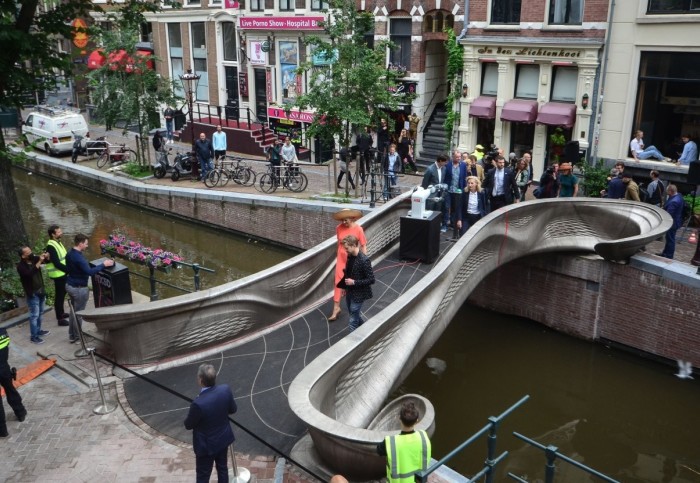
Her Majesty Queen Máxima of the Netherlands opened the bridge

The world’s first 3D-printed steel structure, a ‘living laboratory’ bridge co-developed by Imperial, has been unveiled by Queen Máxima in Amsterdam.
The bridge, which is over four years in the making and was built by Dutch company MX3D, will be a ‘living laboratory’ in Amsterdam’s city centre. It was unveiled in July 2021 by Her Majesty Queen Máxima of the Netherlands.
Using its vast network of installed sensors, Imperial College London researchers will measure, monitor and analyse the performance of the novel 12-metre-long structure as it handles pedestrian traffic.
A 3D-printed metal structure large and strong enough to handle pedestrian traffic has never been constructed before. Professor Leroy Gardner Department of Civil and Environmental Engineering
The data collected will enable researchers and engineers to measure the bridge’s ‘health’ in real time, monitor how it changes over its lifespan and understand how the public interacts with 3D-printed infrastructure.
The data from the sensors will be put into a ‘digital twin’ of the bridge – a computerised version which will imitate the physical bridge with growing accuracy in real time as sensor data come in. The performance and behaviour of the physical bridge will be tested against the twin, which will help answer questions about the long-term behaviour of 3D-printed steel, as well as its use in real world settings and in future novel construction projects.
To get from the conceptual stage to the installed footbridge, the Steel Structures Research Group at Imperial conducted the underpinning research and validation, including testing destructive forces on printed elements, advanced digital twin computer simulations, non-destructive real world testing on the footbridge and the development of an advanced sensor network to monitor the bridge’s behaviour over its life.

Imperial co-contributor Professor Leroy Gardner of the Department of Civil and Environmental Engineering said: “A 3D-printed metal structure large and strong enough to handle pedestrian traffic has never been constructed before. We have tested and simulated the structure and its components throughout the printing process and upon its completion, and it’s fantastic to see it finally open to the public.”
It has been fascinating and we are delighted that the structure is now ready to be used. Dr Craig Buchanan Department of Civil and Environmental Engineering
Imperial co-contributor Dr Craig Buchanan, also of the Department of Civil and Environmental Engineering, said: “We look forward to continuing this work as the project transitions from underpinning research to investigating the long-term behaviour of metal printed structures. Research into this new technology for the construction industry has huge potential for the future, in terms of aesthetics and highly optimised and efficient design, with reduced material usage. It has been fascinating and we are delighted that the structure is now ready to be used.”
The testing work was led by Professor Gardner and Dr Buchanan, supported by a team of undergraduate and postgraduate students, PhD candidates, post-doctoral researchers and laboratory technicians.
The bridge was installed over the Oudezijds Achterburgwal canal in Amsterdam’s Red Light District and was being unveiled on 15 July 2021.
’Tremendous opportunities’
3D printing presents tremendous opportunities to the construction industry, enabling far greater freedom in terms of material properties and shapes. Professor Leroy Gardner Department of Civil and Environmental Engineering
In the absence of structural design provisions for 3D-printed steel, physical testing and computer simulation is important for ensuring the safety of new 3D-printed structures. Imperial's Steel Structures Research Group therefore undertook an ambitious research programme using small-scale destructive material and cross-section testing, computer modelling and large-scale non-destructive real world testing on the footbridge.
Professor Gardner said: “3D printing presents tremendous opportunities to the construction industry, enabling far greater freedom in terms of material properties and shapes. This freedom also brings a range of challenges and will require structural engineers to think in new ways.”
Dr Buchanan said: “For over four years we have been working from the micrometre scale, studying the printed microstructure up to the metre scale, with load testing on the completed bridge. This challenging work has been carried out in our testing laboratories at Imperial, and during the construction process on site in Amsterdam and Enschede, the Netherlands, on the actual printed bridge.”
The Imperial researchers are part of a wider team of structural engineers, mathematicians, computer scientists and statisticians working on The Alan Turing Institute-Lloyd’s Register Foundation programme in data-centric engineering. The programme is led by Professor Mark Girolami at The Alan Turing Institute and previously of Imperial's Department of Mathematics.
Professor Girolami said: “3D printing is poised to become a major technology in engineering, and we need to develop appropriate approaches for testing and monitoring to realise its full potential. When we couple 3D printing with digital twin technology, we can then accelerate the infrastructure design process, ensuring that we design optimal and efficient structures with respect to environmental impact, architectural freedom and manufacturing costs.”
The data captured from the bridge will be made available to other researchers worldwide who want to work with the Turing researchers in analysing the data.

Now the bridge is unveiled, the researchers will begin collecting data in real time to monitor how it behaves.
The team’s work was predominantly funded by The Alan Turing Institute, with additional funding from the Engineering and Physical Sciences Research Council, part of UK Research and Innovation.
Initial bridge design images: Joris Laarman Lab
Other images: MX3D
Research papers published by Imperial academics during the construction and testing of the bridge:
- Testing and initial verification of the world's first metal 3D printed bridge by Gardner et al., published September 2020 in Journal of Constructional Steel Research
- Mechanical and microstructural testing of wire and arc additively manufactured sheet material by Kylevou et al., published July 2020 in Materials & Design
- Metal 3D printing in construction: A review of methods, research, applications, opportunities and challenges by Buchanan & Gardner, published February 2019 in Engineering Structures
Supporters
Article text (excluding photos or graphics) © Imperial College London.
Photos and graphics subject to third party copyright used with permission or © Imperial College London.
Reporter
Caroline Brogan
Communications Division

Contact details
Tel: +44 (0)20 7594 3415
Email: caroline.brogan@imperial.ac.uk
Show all stories by this author
Leave a comment
Your comment may be published, displaying your name as you provide it, unless you request otherwise. Your contact details will never be published.
Comments
Comments are loading...