Materials preparation laboratory
Location: B01
Our wet lab facility contains 16 fume hoods and a range of equipment for chemical synthesis and sample preparation:
- 500ºC Ovens and heating plate
- Spin coater for fabrication of thin films
- Weighting balance
- Ultrasonic horn
- Ultrasonic bath
- Magnetic stirring hot plates
- Glass cutting station
- Welding system
- Doctor blading machine
Device fabrication facilities
Location: LG08, Cleanroom
Device fabrication facilities are housed into a 150 m2 cleanroom of class ISO 7 and 8 (i.e less than 10,000 particles of 0.5 µm size per cubic foot of area). It is particulate controlled area with approximately 30 air exchange per hour and maintained temperature at 21±1°C. The laboratory has a dual light system White and Amber lights compatible for the process that has been essential for white light sensitive materials as well as photolithography processes. Currently the laboratory facilities are used for fabrication of solar cells, transistors and organic light emitting diodes using polymer, small molecule and perovskite materials. Recently the cleanroom has been awared LEAF Gold award for the lab's involvement in driving laboratory sustainability.

1. Glovebox facilities
An extended glovebox system (with 15 hands) contains two thermal evaporators for top electrode evaporation and a spin coater unit for spincoating air and water sensitive small molecule and polymer materials. The system also contains measurement equipment such as a home-built transistor rig enabling us to characterise fabricated transistors made from air and water sensitive organic materials fully without exposing those into ambient environment.
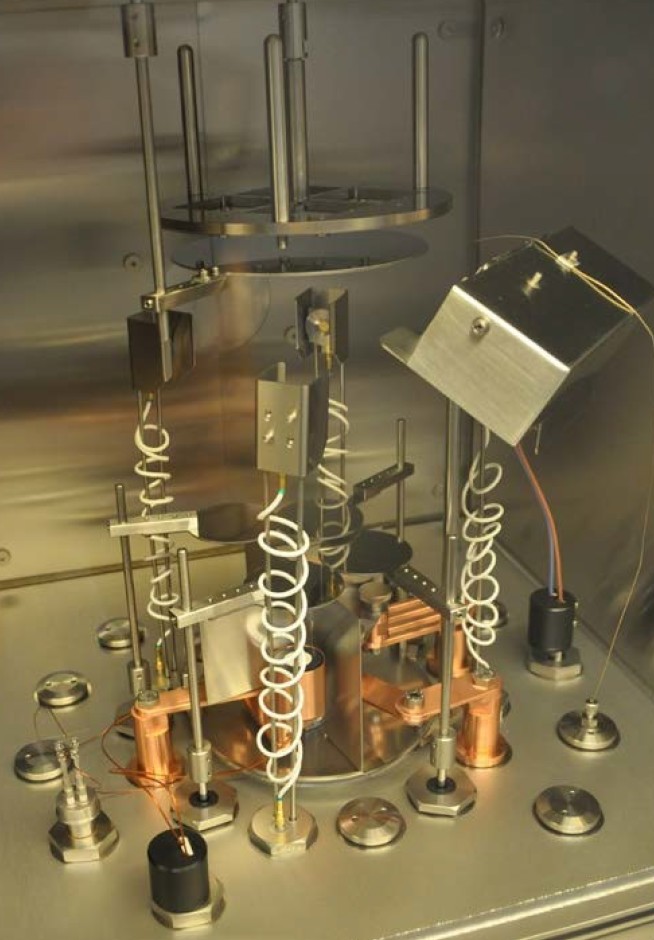
MBraun and Kurt J Lesker evaporators are located inside Mbraun Glovebox for depositing ultra-thin and thin electrodes onto the active layer through a patterned shadow mask to complete off device. The interface materials such as Lithium fluoride, Calcium, Magnesium, Molybdenum trioxide and metals such as Silver, Aluminium, Gold, Chromium, Copper are thermally heated and deposied on the active layer at low vacuum 3 x10-6 mbar ensuring a highly accurate evaporation rate and device reproducibility.
This state of art organic small molecule and polymer materials device fabrication area enable users to fabricate optimum devices upto 15% power conversion efficiency.
2. Perovskite Glovebox facilities
Perovskite material and device fabrication is done in the dedicated area in the cleanroom. The facilities consistes of Mbraun labstar glovebox and the recircuting fumehood only for handling perovskite materials.
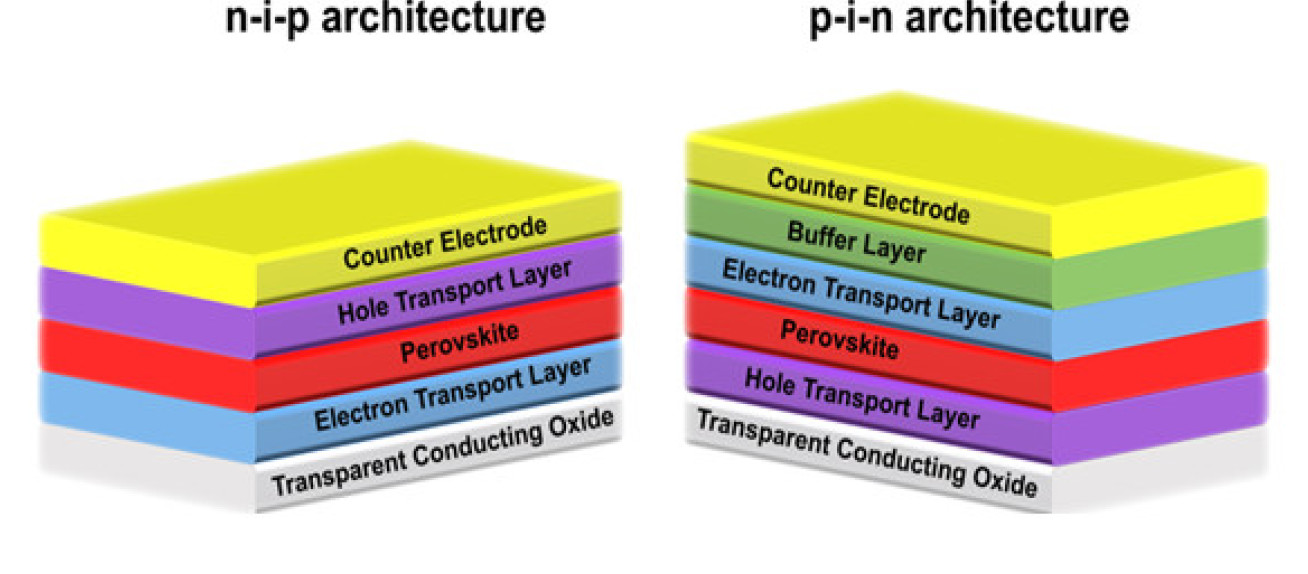
Both n-i-p and p-i-n perovskite solar cells are fabricated in the group as shown here
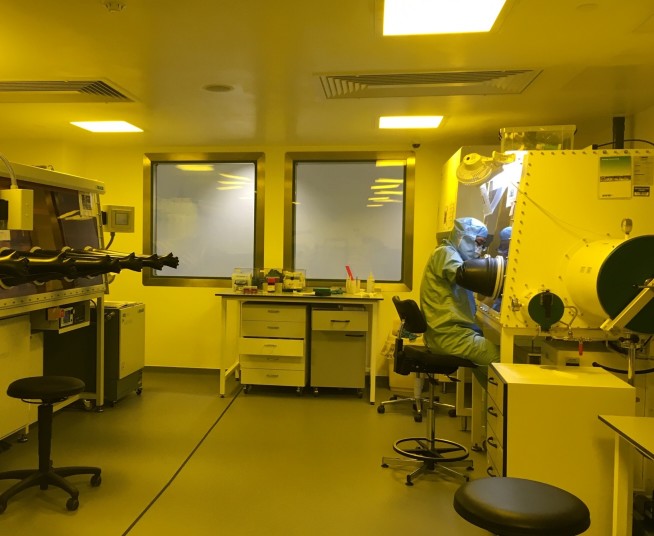
Handlings such as weighing and making solution of perovskite materials are done either into the dedicated perovskite glovebox or inside an operating recircuiting fume hood. All users must ensure the recirculating fumehood meets all essential compliances for users protections before using it. The spincoater in the labstar glovebox is provided with a programmable 3.5” touch panel capable of a manual and semi-automatic coating of thin layer up to substrate size of 8”X8”. The annealing of films are done in the same glovebox using a programmable hotplate. This state of art facilities enable us to fabricate upto 20.4% effcient perovskite solar cells.
In addition to the cleanroom training, the perovskite area users will receive extensive health and safety training due to nature of perovskite material before accessing this area and facilities in there.
3. Wet laboratory fabrication facilities
The wet fabrication facilities is used for preparation of blend solutions of small molecules and polymer materials for making films of active layer for the device fabrications and other studies.
Chemical work stations and hoods
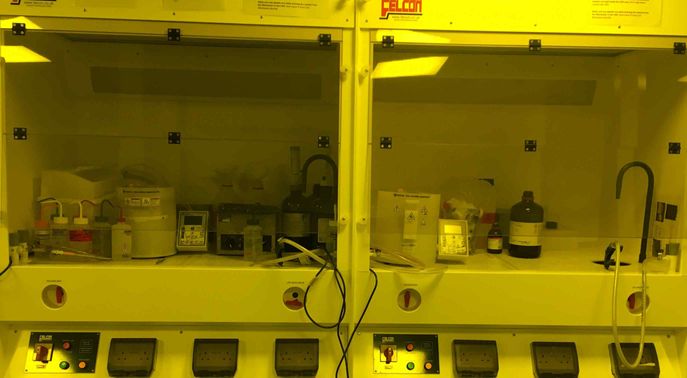
Chemical workstations
The chemical workstations in Wet lab are compatible for all wet chemistry such as ultrasonic cleaning of different types of substartes and preparation of small organic molecule and polymer blend solutions. The deposition of water and alcohol-based interfaces are also spincoated in the chemical workstations.
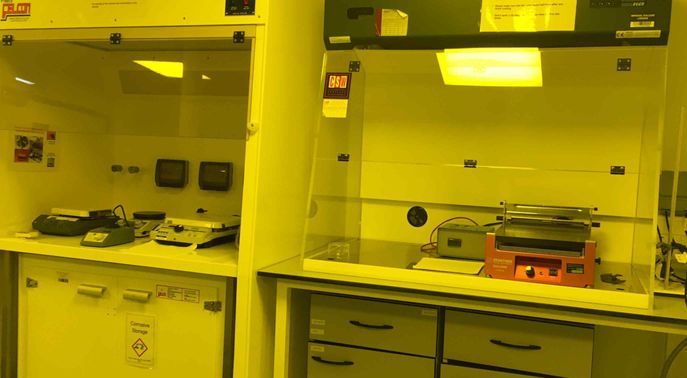
Laminar and recirculating fume hoods
Handling such as weighing or making solution and using a barcoater for coating films are done into the recirculating fume hoods. Hot plates with different specifications are kept into the laminar flow hood for annealing water and alocohol based interfaces.
The wet fabrication facilities contains following facilities and equipments:
- Ultrasonic baths
- Diener Femto Oxygen plasma system
- Spincoater dedicated only for polymers
- Spincoaters dedicated for water and alcohol based materials
- Analytical balances
- Hotplates and stirrers with different specifications
- Zehntner and RK Bar and knife coaters for coating solutions on bigger substartes
- Alpha step Tencor D500 surface profilometer
- Contact angle measurement unit
- Four point probe sheet resistivity measurement unit
Device fabrication tools
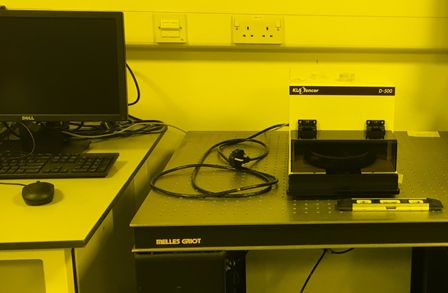
Alpha Step Tencor D500 Surface Profilometer for measuring thickness of thin films ranging from 5nm to 120μm
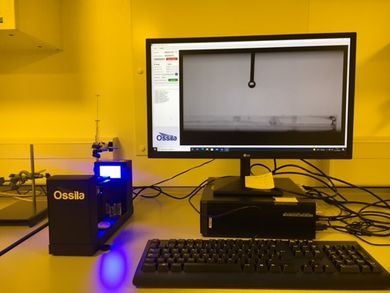
Contact angle measurement unit with a rapid image capture for in-depth image analysis and high resolution (1920x1080, 30 fps) images

Diener Femto oxygen plasma chamber-treating substrates at different oxygen pressure from 0.1mbar to 5mbar at different time from few seconds to minutes
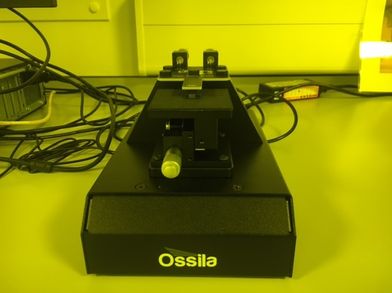
Four Point Probe- Sheet Resistance Measurement unit with a single probe with four linear probes with 1.27 mm spacing between, 0.48 mm probe diameter, and 60g spring pressure- non invasive and no damage to films and capable of measuring between 100 mΩ/□ and 10 MΩ/□
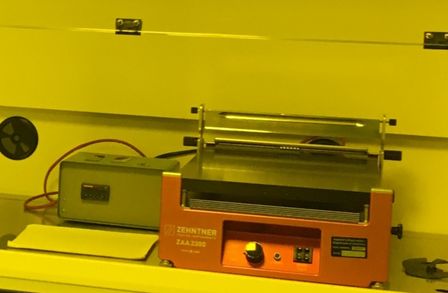
Zehntner bar coater ZA2000 for coating films of polymer with thickness variation from 0 μm to 3,000 μm