Projects I
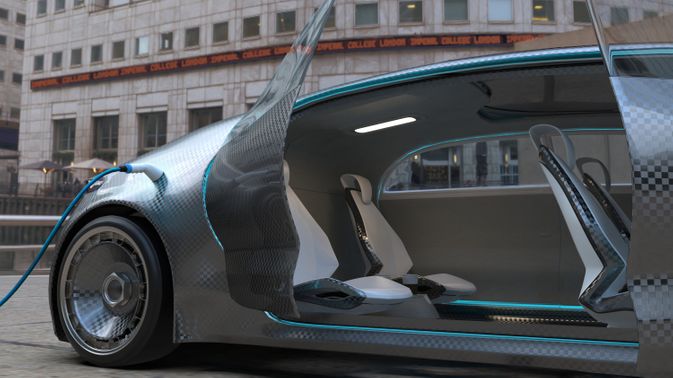
Realising Structural Battery Composites
The proposed research by Chalmers, KTH and Imperial College London (ICL) aims at the development and demonstration of a multifunctional material that can simultaneously store electrical energy and carry mechanical loads. We have coined this material as structural battery composite. Structural batteries will allow radical weight savings for any electrically powered structural system, from mobile phones to aircraft. Over the last decade, the three universities have performed research to realise structural battery composites. Current structural battery composites have demonstrated an energy density of 24 Wh/kg at a Young's modulus of 25 GPa. In the proposed project we seek to develop and demonstrate a second-generation laminated structural battery composite with an energy density of 100 Wh/kg and an in-plane modulus (isotropic) of 40 GPa. This is slightly lower than traditional Li-ion batteries and composites but combined into a multifunctional material provides significant mass savings.
The structural battery composite is made from carbon fibre reinforced electrodes in a structural electrolyte matrix material. Neat carbon fibres are used as the structural negative electrode, exploiting their high mechanical properties, excellent lithium insertion capacity and high electrical conductivity. Lithium iron phosphate coated carbon fibres will be used as the structural positive electrode. The electrodes are to be separated by an ultra-thin fibrous separator.
The project is funded by the US Airforce via its European Office of Aerospace Research and Development.
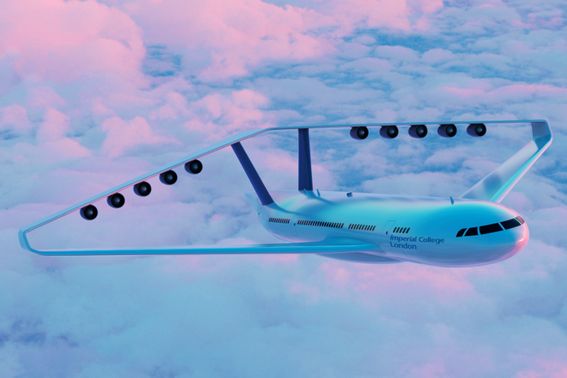
Realising Structural Power
Research into multifunctional composites that store electrical energy and structural power can make a significant impact in delivering new technologies and training engineers to address the future societal challenges associated with energy storage and lightweighting.
The breadth of potential applications and the simplicity of the concept of structural power has drawn considerable interest from academia, industry and the public to our work. However, it is apparent that there is a need for practical demonstrators with defined performance parameters before industry can consider adopting this technology for their own products. Although structural power straddles two critical technologies (polymer composites and energy storage), the developments to date have been driven by the Composites Sector, which is currently undergoing phenomenal growth, compelled by widespread adoption in sectors such as Automotive.
To maximise the impact, we have drawn together material suppliers, research institutes and end-users who will form the industrial advisory board and include Airbus, Hexcel Composites, Hive, BAE Systems, Gen2Carbon, NCC, NPL and CME. Importantly towards the culmination of the project they will inspire our demonstrator selection by identifying applications for early adoption of this technology.
Realising Structural Power is funded by a UK Research and Innovation research grant.
Projects II
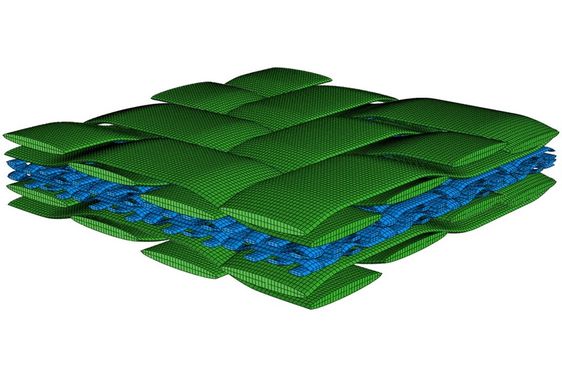
EPSRC Future Composites Manufacturing Research Hub
Building on the success of the EPSRC Centre for Innovative Manufacturing in Composites (CIMComp) the Hub consortium has 15 UK academic partners, a further 23 international academic partners, and currently 40 industrial partners. The main focus of the Hub is the step-change approach to composite manufacturing, this is split into five research priorities which includes the Manufacturing for multifunctional composites and integrated structures of which Imperial College London and University of Bristol have a collaborative Core Project.
One specific focus over the past year was to develop a viable method to enable structural power composites to be manufactured with complex geometries. Currently, the rigid CAG reinforcement used to enhance both mechanical and electrochemical performance hinders formabililty over a tool. Overcoming this challenge paves the way for structural power composites to be used in a much greater range of applications than would otherwise be possible.
The Future Composites Manufacturing Hub is funded by a UK Research and Innovation research grant (EP/P006701/1).
For further information please visit the project website CIMComp.
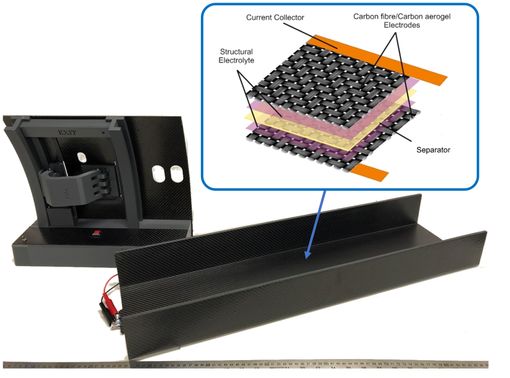
The Structural pOweR CompositEs foR futurE civil aiRcraft (SORCERER)
A close collaboration between four European Universities; Chalmers (Sweden), IMDEA (Spain), Imperial College London (UK), and KTH (Sweden). We aim to enhance the electrical and mechanical performance of our, already develop state of the art, multifunctional materials towards practical implementation. In addition to improving absolute multifunctional performance, we are resolving issues related to systems integration and scale-up. The culmination of the SORCERER project will be the implementation of our structural power composites in an industrially focused demonstrator in association with Airbus, Chomarat and TeXtreme, with additional support from BAE Systems, Hexcel, and QinetiQ.
The project is developing two complementary approaches. Structural supercapacitors offer high power densities and maximum stability, whilst structural batteries offer maximum energy density. In principle, the two electrochemical systems can be combined to respond to a range of electrical load demands.
SORCERER is funding by EU Horizon 2020 Programme (H2020-EU.3.4.5.1. #738085) which is part of the Clean Sky2 Funding Scheme (CS2-RIA - Research and Innovation action), with support from Airbus, Chomarat, TeXtreme, BAE Systems, Hexcel and QinetiQ.
For further information please visit the project website SORCERER.
Related links
Contact
Professor Emile S Greenhalgh
Department of Aeronautics
Imperial College London
South Kensington Campus
London SW7 2AZ
+44 (0)7958 210 089
e.greenhalgh@imperial.ac.uk