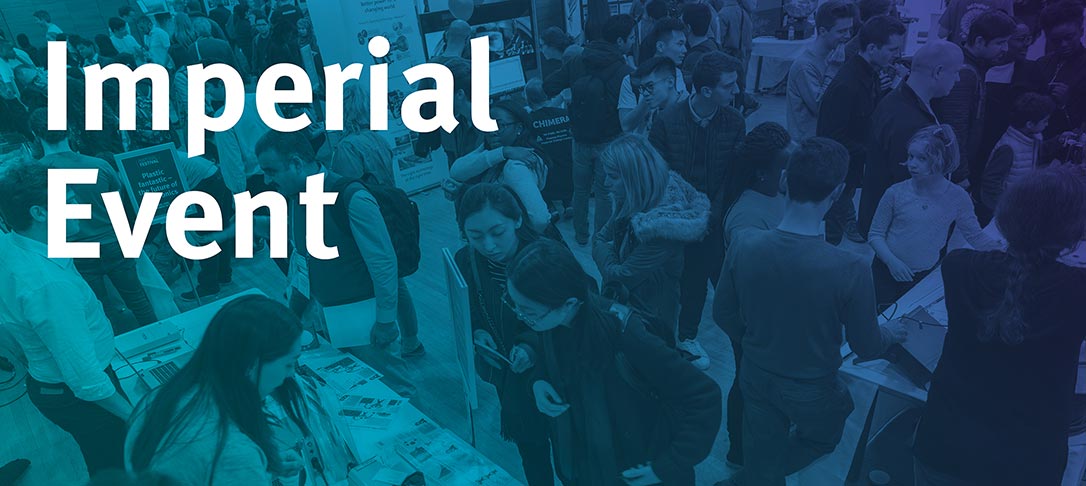
Abstract: Microfluidic phenomena associated with droplets and bubbles influence the performance and effectiveness of large-scale industrial processes involved in energy production, water treatment and carbon capture-sequestration. Surface engineering (control of texture and chemistry) and electric fields are powerful tools to control droplets and bubbles, and favorably impact process phenomena. This talk highlights recent advancements from the author’s group in three areas: i) CO2 hydrate production for carbon sequestration, ii) electrocoalescence for process intensification, and iii) electrowetting heat pipes for long-distance heat transport.
CO2 hydrates are ice-like crystalline solids which form under medium pressure and low temperature conditions from water (cage of host molecules) and gas (guest molecule). The ability to lock-up environmental CO2 as CO2 hydrates on the seabed is a promising option for sequestering the expected 10 gigatons/yr CO2 by 2050. A significant technological barrier to any technology involving hydrates is the sluggish rate of formation of hydrates, which can be attributed to thermodynamic and kinetics-related limitations. Recent efforts in my group have uncovered multiple techniques to speed up hydrate formation by one-two orders of magnitude. These techniques intensify the mass and heat transfer associated with hydrate formation and include gas bubble sparging, electronucleation, use of metal catalysts, and high thermal conductivity foams.
The second topic is about controlling droplet microfluidics via surface engineering and electric fields; this has vast applications in steam condensation, separations and other process phenomena in the chemical industry. Electric field-promoted dropwise condensation of water will be discussed along with its impact on condensation heat transfer. The use of electrocoalescnece in promoting oil-water separation will also be discussed.
The third topic is about a new concept for a heat pipe (device to transport heat via evaporation-condensation of working fluid). An electrowetting heat pipe (EHP) relies on electrical pumping of condensate instead of wick-based pumping in conventional heat pipes. This switch enables the development of heat pipe architectures that can move high (kiloWatt) heat loads over long distances. The microfluidics underlying such an EHP was characterized on the International Space Station in 2017.
Bio: Dr. Vaibhav Bahadur (VB) is an Associate Professor and Carl J. Eckhardt Fellow in Mechanical Engineering at UT Austin. His research interests lie in thermal sciences, materials, micro/nanofabrication and machine learning. He conducted fundamental and applied research in these area with applications in energy-water systems, microelectronics thermal management and carbon-capture sequestration. Prof. Bahadur has a PhD in Mechanical Engineering from Purdue University and a Postdoc from Harvard University. Additionally, he has 4 years industry R&D experience in GE Global Research and Baker Hughes. Prof. Bahadur is the recipient of the NSF CAREER Award (2017), the SPE Petroleum Engineering Young Faculty Award (2015), the ASME ICNMM Outstanding Early Career Award (2018), the Google Faculty Research Award (2018), and the ACS Doctoral New Investigator Award (2014). He is the winner of the Society of Petroleum Engineer’s R&D Competition at SPE Annual Technical Conference and Exhibition (2014). Technology developed in his lab was tested on the International Space Station in 2017. Prof. Bahadur has authored 60+ journal articles (h-index of 27), 35+ articles in conference proceedings, 1 book chapter, and has 8 patents issued or pending