How is research in the Mechanics of Materials division making a difference in the real world? Here are a few case studies:
2 col general content block
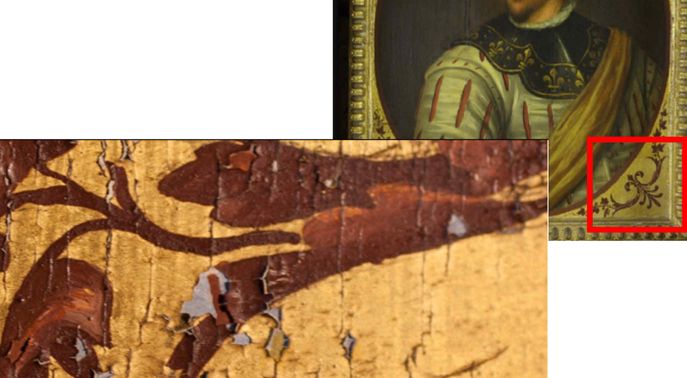
Mechanisms of cracking in 17th century oil paintings on wood
Panel paintings are an example of painted wooden cultural heritage that can suffer irreversible damage due to variations in their storage environmental conditions. Understanding what conditions cause paintings to crack is of extreme importance as cracking results in a loss of paint, and consequently, a loss of the aesthetic of the work, interpretation and appreciation by the viewer.
Through a combination of modelling and experiments, the work aims to investigate the initiation and propagation of cracks due to changes in environment, and predict suitable conditions to preserve this cultural heritage.
Project team: A joint collaboration between Imperial College London (Joseph D. Wood, Daniel S. Balint, Ambrose C. Taylor, Maria, N. Charalambides) and University of Glasgow (Cecilia Gauvin, Christina R.T. Young).
Timeline: The three year project commenced in February 2017.
Sponsors/partners: EPSRC (Engineering and Physical Sciences Research Council), The National Trust, The National Gallery, Akzo Nobel
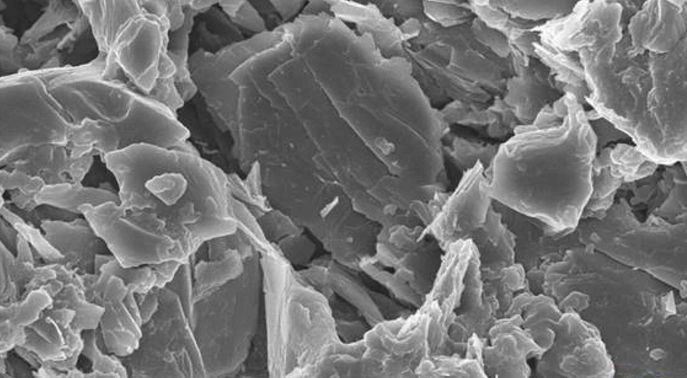
Battery Advances for Future Transport Applications (BAFTA)
Battery pack design has historically been empirical – make it and see how well it works. The aim of the BAFTA project is to change that process by developing a toolkit of models, software and methodologies, based on fundamental and applied science. These will be used for two purposes: the design of the battery pack including cell selection, pack configuration, thermal management and degradation predictions; and the battery management system which monitors the state of available power, state of charge, and state of health. The outcome will allow the project partners to develop high performance battery packs whilst preserving battery lifetime.
Project team: A joint collaboration between Imperial College London (Teddy Szemberg O’Connor, Jingyi Chen, Billy Wu, Yatish Patel, Ricardo Martinez-Botas, Gregory Offer), Aston Martin Lagonda, and Dukosi.
Timeline: The 30 month project commenced in September 2018.
Sponsors/partners: Aston Martin Lagonda, Dukosi. The project is funded by Innovate UK, as part of the Faraday Battery Challenge
2 col general content block 2
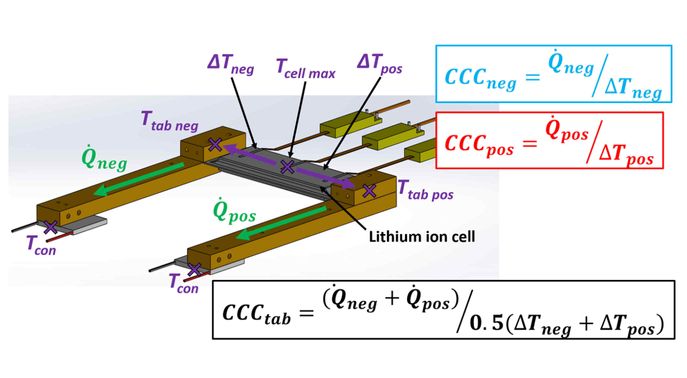
Developing isothermal testing equipment
for testing automotive lithium-ion batteries
Every battery parameter is affected by temperature. Therefore, it is essential to have very precise temperature control when parameterising any battery. This is especially important in the automotive industry, where batteries generate a lot of heat. The project aim is to design bespoke laboratory equipment that can control temperature to far greater precision than can be achieved at present. Armed with this equipment, automotive companies will be able to understand their batteries’ performance far better. This will reduce the cost and increase the lifetime of electric vehicles.
Project team: A joint collaboration between Imperial College London (Alastair Hales, Yatish Patel, Gregory Offer), Cranfield University and Thermal Hazard Technology.
Timeline: The 18 month project commenced in July 2019.
Sponsors/partners: Thermal Hazard Technology. The project is funded by Innovate UK, as part of the Faraday Battery Challenge
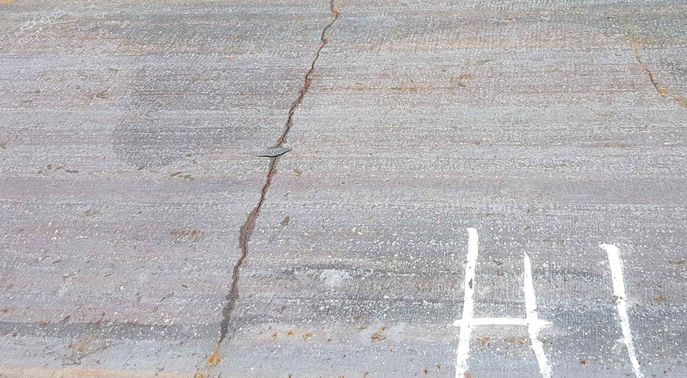
A fundamental understanding of clinking
during the cooling and reheating of as-cast steel slabs
A fracture event called ‘clinking’ occurs in the steel making process at Tata Steel’s Port Talbot plant. During this process, steel slabs weighing over 13 tonnes break apart whilst cooling in a slab yard after casting. If one of these fracture events occur, process interruptions and material losses can cause financial losses to the plant into the millions of pounds. It is important to steel manufacturers to understand why certain compositions fracture when others do not, and more importantly, how to alleviate and predict this fracture event through controlling thermal cycles during casting, cooling and reheating. An understanding of the key causes of clinking will give manufacturers the ability to produce and refine compositions and processing of steels whilst alleviating clinking.
Timeline: The 3 and a half year project commenced in July 2016 and finished in February 2020.
Sponsors/partners: EPRSC (Engineering and Physical Sciences Research Council), Tata Steel UK
2 col general content block 3
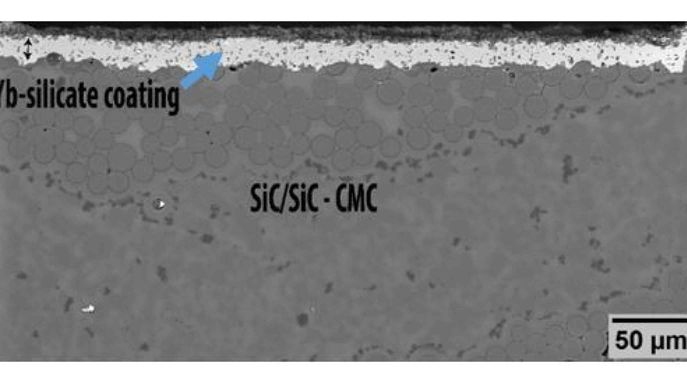
Adhesion strength of environmental barrier coatings
on SiC/SiC CMCs for aerospace application
Silicon carbide fibre reinforced ceramic matrix composites (SiC/SiC CMC) are state of the art materials to substitute alloys in aerospace industry, with advantages of weight saving up to 30% due to their low density, improved fuel consumption and reduction of NOx emmision and increased service lifetime. CMC materials undergo accelerated oxidation in the high temperature environments found in a gas turbine. To prevent such accelerated oxidation and premature component failure, environmental barrier coatings (EBCs) are required to limit the access of oxygen to CMC surfaces. A variety of EBCs have been developed in the past consisting of a minimum of 4 layers requiring a costly application method such as plasma spraying. The aim of the project is to understand the adhesion strength at the interface of a single layer of coating at the interface of a substrate to predict accurately the service life of the coating and ensure they survive their design conditions.
Project team: R. Kassem, N. Al Nasiri and Maria, N. Charalambides, Imperia College London.
Timeline: The three and half year project commenced in December 2019.
Sponsors/partners: EPSRC (Engineering and Physical Sciences Research Council) and Rolls Royce plc.
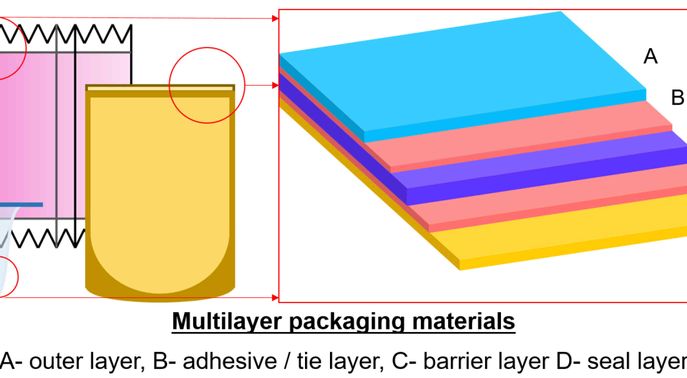
Mechanical Recycling of multilayer packaging materials (MLP)
Multilayer packaging (MLP) films are utilised predominantly in the food industry to extend the shelf life of food articles. Currently, these packaging materials are landfilled or incinerated after their use as there are many inherent challenges that needs to be addressed to enable their recycling. The Soft Solids group’s research activities in this space includes developing material models to predict the mechanical properties of recycled MLP from combined melt processing. These models can offer a virtual testing platform for the optimisation of recycled materials and their mechanical properties, greatly reducing the need for alternative trial-and-error approaches. Additionally, tapping into the group’s extensive experience on adhesion, new recycle-friendly multilayer packaging designs are also being investigated to mitigate the challenges limiting the recyclability of MLP while preserving the value of recycled materials from MLP.
Project team: Investigators: Daniel Balint, Bamber Blackman, Maria Charalambides, Soraia Pimenta, Ambrose Taylor. PDRA: Manu Charles Mulakkal
Timeline: Project due to end December 2020
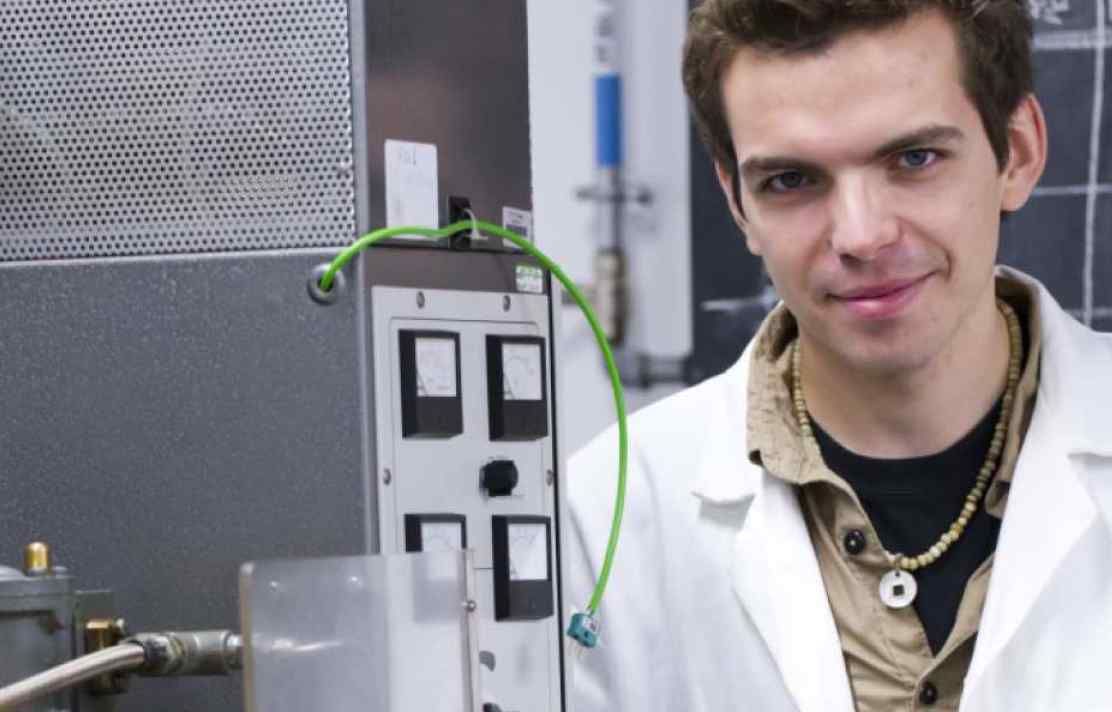
PhD study
Early Career Research Fellowships
Find out more about applying for early career fellowships in our department