Adventures in... 3D printing
A revolution in construction is taking place – right beneath our feet.
Words: Helena Pozniak / Photography: Adriaan de Groot
Next year a bridge will appear in the middle of Amsterdam unlike anything ever seen before. Sleek, undulating and futuristic, it is a world first: it was created by 3D-printing robots.
“We could never have imagined this would be possible, even a few years ago,” says Professor Leroy Gardner (MSc Civil and Environmental Engineering 1999, PhD 2002) at the Department of Civil and Environmental Engineering. “3D printing opens up the opportunity to produce weird and wonderful shapes – you can put the material just where you want it. Nothing like this has been done before.”
But while it has been fascinating to watch the molten steel take shape in an Amsterdam factory, the main priority for Gardner and his team has been to ensure that pedestrians and cyclists in the Dutch city will be safe on this radical new design.
Indeed, the team have been compressing the 3D-built steel to see if it buckles under the same loads as traditional steel, stretching it to understand how it deforms and loading containers with water on to the bridge to check the structure is sturdy enough to take the weight of pedestrians.
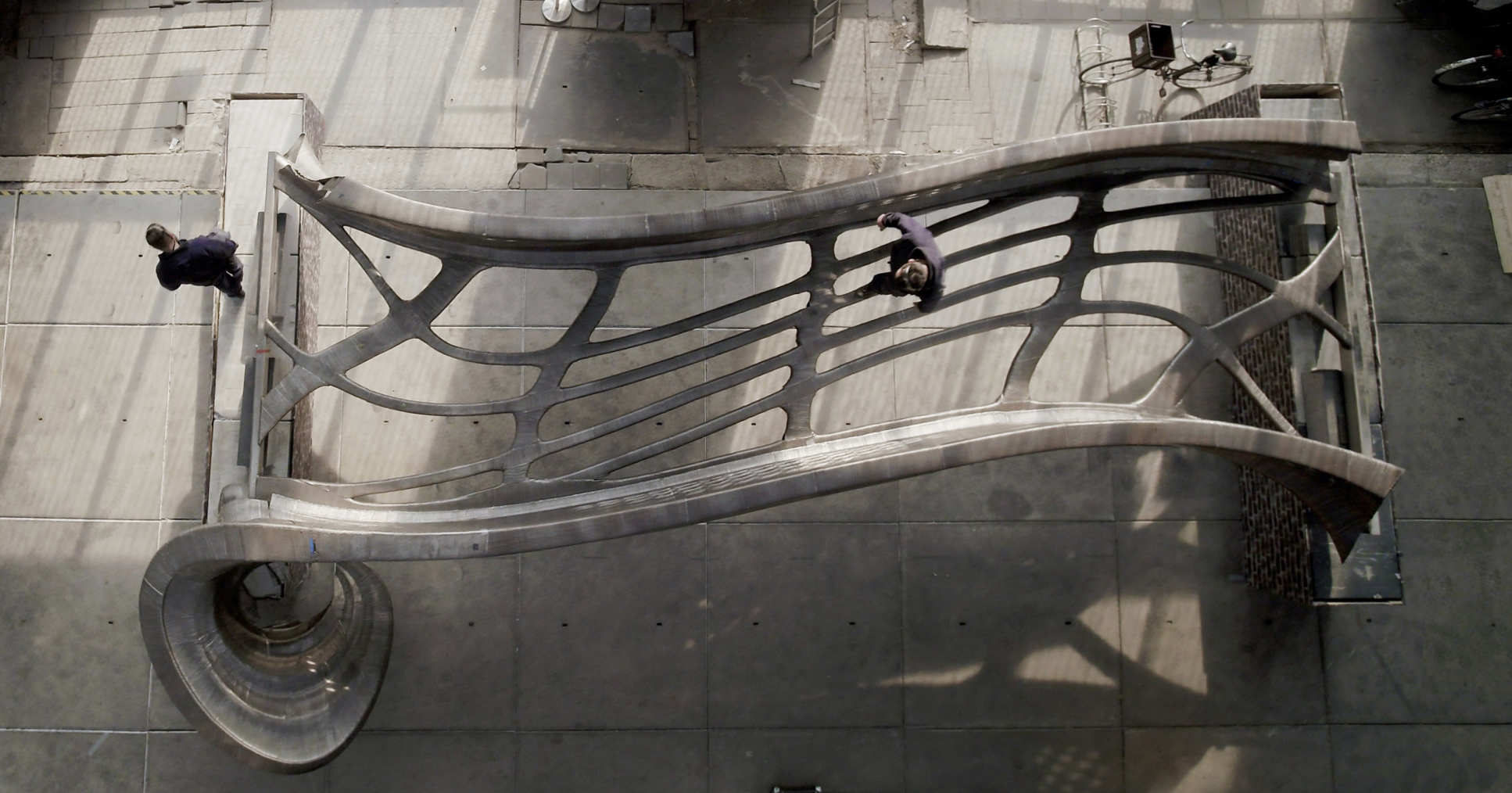
In the process, they have discovered that 3D steel has a rather curious property – it is anisotropic, which means its physical properties vary in different directions, because of the way layers are built up. “It has an inherent directionality, depending on whether you load the material parallel to the layers or across them. As an engineer, you need to understand that,” says Gardner. By contrast, traditionally manufactured steel is essentially isotropic – with the same mechanical properties in all directions.
Meanwhile, data scientists at Imperial plan to measure the 12-metre bridge as never before, with a vast network of sensors. “We’ll be able to gauge its ‘heartbeat’,” says Professor Mark Girolami, from the Department of Mathematics and an expert in how big data can be incorporated into engineering practice. He’s based at the pioneering Alan Turing Institute, which specialises in data-centric engineering, and his team is working with engineers and the Dutch 3D-printing company, MX3D, which is behind the design and production of the bridge.
Sensors will measure vibrations, stress on different parts of the structure and ambient temperature – giving data scientists a wealth of information that they will use to inform a virtual model of the bridge and assess how it performs. Scientists will feed data from the real bridge into its virtual copy – created from a 3D laser scan. “We call it a ‘digital twin’,” says Girolami.
“This is new material and there’s a lot we don’t know about its properties. Having one structure learn from the other – the real and the digital – could be revolutionary.” In this way, scientists will be able to predict how the structure will behave in the future.
“What makes this exciting is that we will have a living laboratory on our hands,” says Girolami. “We’ve not seen this level of integration of sensors and cameras before. We might also be able to measure social behaviour and what impact the bridge has on the surrounding area.”
While printing a bridge in this way may not be the fastest or cheapest way to build, it has enormous potential.
“We are pushing the boundaries, and when it comes to 3D printing in construction, this may well be just the start,” says Girolami. “Architects love this style of manufacturing. Normally we have to rein them in, but this gives so much freedom.”